Country
UK
Application
Process water
Water source
Lagoon
Filtration solution
AFM glass media
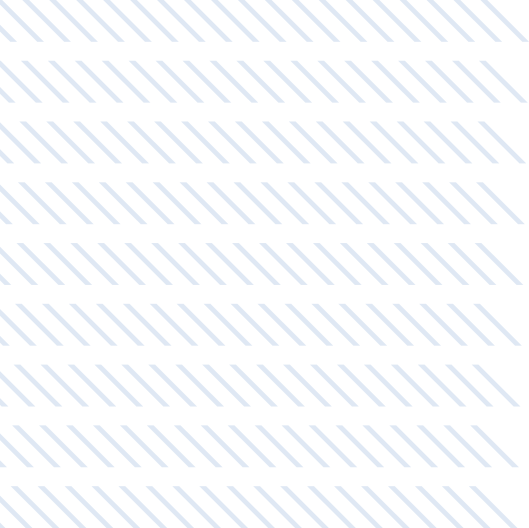
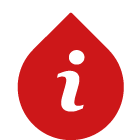
Background
One of the largest steel producers in Europe contacted Amiad with a brief of updating their current sand filters situated at their cold mill rolling plant in South Wales, UK.
The sand filters were not performing to the minimum standard required and water quality was poor as a result.
This led to a lot of downtime with the filters and decreased processed water for production.
Although losing one or two of the sand filters for a short time whilst it was worked on was acceptable in the short term, increased production started to put a strain on the capability of the system in general to facilitate usable water for the cold mill.
This inevitably resulted in a vastly inflated increase in water usage which escalated the plant production costs significantly.
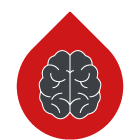
Challenge
The water being processed was drawn from the lagoon onsite and passed through the sand filters before going on to the cold mill rolling plant. The lagoon water being extracted resulted in the sand in the filters frequently becoming blocked and thus starting a lengthy and time consuming effort to get them cleaned and back online again.
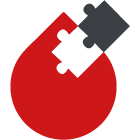
Solution
After various site visits and water sampling to verify the challenges on site, Amiad UK came up with a detailed plan to upgrade the system. This would involve upgrading the existing filtration system to the advanced AFM glass media as utilized in our sub 10 micron DVF filter range.
Included in the proposal was the option of upgrading the media retention nozzles, if required on inspection, after the sand had been removed from the vessels. There was no information available on the nozzles present in the filters prior to the removal of the sand media, and if there were nozzles being used or lateral pipework.
Because of the different properties in terms of bulk density between the sand that was being used and the proposed glass that was to be used in the filters, it wasn’t simply a case of replacing one media with the other. The new glass media would require a different backwash and settling regime to be incorporated into the control philosophy. Additionally, the nozzles or laterals would need to be inspected for purpose and repaired or replaced, dependent on our findings. If the nozzles or lateral filtration design in the plate of the filters was of an old technology and exact replacements could not be obtained to replace individually damaged units, it would be likely that the individual vessel would have to be updated so there would be no areas of preferential flow due to orifice size variation.
After the media was removed it revealed that there were nozzles present in the vessels and that a number of them were damaged and new ones were ordered to replace them. These nozzles were fitted into lateral pipework on the vessel bed plate and some of the internal pipework was also replaced.
When all the repairs had been carried out, the vessels were partly fluidized before the gravel support layer was introduced to protect the nozzles. When this was finished the remaining two layers of Grade 2 and Grade 1 AFM glass media were loaded into each vessel at a pre-determined level. Specially designed orifice plates were retrofitted to the backwash line to reduce the flow facility for backwash operation and the backwash flow valves were reset to the appropriate flow rate at commissioning.
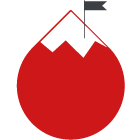
Results
After various site visits and water sampling to verify the challenges on site, Amiad UK came up with a detailed plan to upgrade the system. This would involve upgrading the existing filtration system to the advanced AFM glass media as utilized in our sub 10 micron DVF filter range.
Included in the proposal was the option of upgrading the media retention nozzles, if required on inspection, after the sand had been removed from the vessels. There was no information available on the nozzles present in the filters prior to the removal of the sand media, and if there were nozzles being used or lateral pipework.
Because of the different properties in terms of bulk density between the sand that was being used and the proposed glass that was to be used in the filters, it wasn’t simply a case of replacing one media with the other. The new glass media would require a different backwash and settling regime to be incorporated into the control philosophy. Additionally, the nozzles or laterals would need to be inspected for purpose and repaired or replaced, dependent on our findings. If the nozzles or lateral filtration design in the plate of the filters was of an old technology and exact replacements could not be obtained to replace individually damaged units, it would be likely that the individual vessel would have to be updated so there would be no areas of preferential flow due to orifice size variation.
After the media was removed it revealed that there were nozzles present in the vessels and that a number of them were damaged and new ones were ordered to replace them. These nozzles were fitted into lateral pipework on the vessel bed plate and some of the internal pipework was also replaced.
When all the repairs had been carried out, the vessels were partly fluidized before the gravel support layer was introduced to protect the nozzles. When this was finished the remaining two layers of Grade 2 and Grade 1 AFM glass media were loaded into each vessel at a pre-determined level. Specially designed orifice plates were retrofitted to the backwash line to reduce the flow facility for backwash operation and the backwash flow valves were reset to the appropriate flow rate at commissioning.