Country
Israel
Application
Pre-filtration to UF
Water source
Process Water
Filtration solution
Stage 1: 4 x 2" Spin Klin™ , 70μm
Stage 2: 4 x 2" Spin Klin™ , 50μm
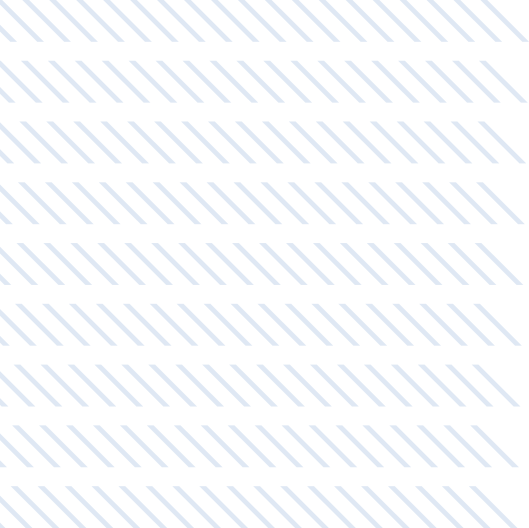
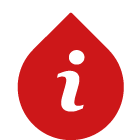
Background
Dairy factories use caustic soda (NaOH) for cleaning the pipes and equipment for cleaning the pipes and equipment on the production floor (CIP). This CIP process of caustic soda (pH 12-14) is a built-in process of the production line and is necessary in order to prevent contamination of the dairy products. The CIP stream flows through all of the production floor pipes and machinery and collects the accumulated precipitant inside the pipes.
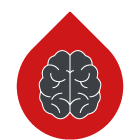
Challenge
The customer’s goal was to filter the precipitant collected by the CIP process, and protect the NF membranes that often get clogged by biofouling. By doing this, the customer will be able to recycle the CIP solution and use it again in the CIP process, thus reducing chemical consumption and lowering chemical discharge as well as to save expenses of the NF membrane filter. The customer was looking for an industrial long-lasting automated solution that complies with the CIP solution properties (high pH, high salinity, etc.).
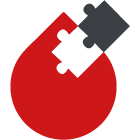
Solution
In 2004, when the customer received high spec, high cost offers from competitors, they continued their search and contacted Arkal (Amiad today). Arkal offered a long lasting, cost-effective solution based on its polymeric filters – 4 units of 2″ Spin Klin™ (70μm) followed by 4 units of 2″ Spin Klin™ (50μm) for a flow rate of 45m3/h (198 gpm) at 1-2 bar (14.5-29 psi), hot water (40˚C) external source air-aided backwashing. This solution benefits the customer by increasing the CIP stream recovery, lower NaOH replacement, minimum BW volume discharge. At the same time, it helps the customer to keep the disc filter maintained for a long period of time.
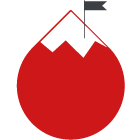
Results
During 2018 and after 15 years of operation, the filtration system was tested according to ISO 18471 (Verification of filtration degree).